What is Iron and How is it Produced?
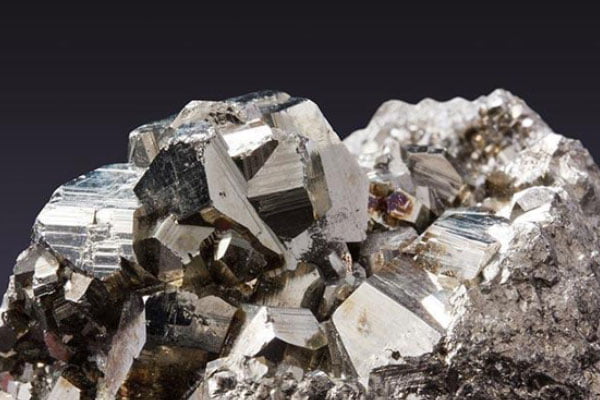
What is Iron?
Iron is a metal found in nature, typically combined with oxygen. Pure iron is a soft, grayish-white metal. Although iron is an element, it is rarely found in its pure form in nature. It is one of the most abundant elements on Earth, and its ores often contain oxygen, silicon, manganese, phosphorus, and sulfur. Iron is also a ferromagnetic metal, meaning it is magnetic and can attract other ferromagnetic metals.
Globally, the largest iron ore reserves are found in Australia, Brazil, China, India, Russia, and the United States. In Turkey, iron ore reserves that are suitable for integrated steel mills are located in the Sivas-Erzincan-Malatya, Kayseri-Adana, Kırşehir-Kırıkkale-Ankara, and Balıkesir regions.
What Are the Steps of Iron Production?
Iron production involves preparing the raw materials that will be fed into a blast furnace. These include iron ore, coke (a type of coal), and limestone.
- Ore Preparation:
Ores that contain more than 60% iron are smelted in a blast furnace. Ores with lower iron content are first crushed and ground into a powder, then concentrated through flotation. The concentrated ore is then shaped into pellets and heated in a furnace. - Coking:
Coal is heated in the absence of oxygen to produce coke, which is used as both a fuel and a reducing agent during the iron-making process. - Blast Furnace Process:
A mixture of iron ore, limestone, and coke is loaded into the blast furnace. Air is blown into the bottom of the furnace, causing the coke to burn. The heat from this combustion melts the iron ore and initiates a reduction reaction. The oxygen in the iron ore is reduced, turning it into molten iron. - Extracting the Molten Iron:
Molten iron and slag (waste material) are drained separately from the bottom of the blast furnace. The molten iron is then poured into molds of the desired shape and size, where it cools and solidifies. - Processing and Casting:
The iron obtained can be used for casting or further processed to produce various products.
The result of this process is pig iron. Further refining steps can turn this iron into steel or other iron alloys by combining it with various elements.
What Are the Uses of Iron?
Iron has a wide range of applications. Its most common use is as the main component in steel production. Steel is made by alloying iron with carbon and other elements to enhance its properties.
- Pig iron, which has a high carbon content, is often used in casting applications. Due to its excellent castability, pig iron is used to produce complex machine parts, engine blocks, pipes, and radiators.
- In the construction industry, iron is used to produce steel reinforcements for reinforced concrete structures. It is also used in the production of load-bearing systems like bridges, rails, and structural components.
- Iron plays a crucial role in the production of magnets because it is naturally magnetic.
- In the automotive industry, iron is used to manufacture certain engine parts and chassis components.
What is the Difference Between Cast Iron and Wrought Iron?
Iron, after being extracted and processed, is typically used as either cast iron or wrought iron. Though both are made from iron, they are not the same.
What is Cast Iron?
Cast iron is an iron alloy containing approximately 2-4% carbon, along with trace amounts of silicon, manganese, and other elements. It is called “cast iron” because it is shaped through a casting process.
To produce cast iron, pig iron is melted and mixed with carbon and other alloying elements. The molten iron solution is then poured into molds of various shapes. Once cooled, it solidifies into cast iron, ready for use.
Cast iron is often used for products such as heating radiators, fireplaces, gutters, poles, and lampposts. However, due to its brittleness and tendency to rust, many of these uses have been replaced by other materials, though cast iron objects are still made for their aesthetic qualities.
What is Wrought Iron?
Wrought iron, on the other hand, contains 1-2% slag, a byproduct of the smelting process. The slag in wrought iron typically consists of elements like silicon, phosphorus, and sulfur.
To make wrought iron, the iron is repeatedly heated, bent, and shaped. The process of repeatedly heating and working the iron strengthens it.
Differences Between Cast Iron and Wrought Iron:
Aside from their compositions, there are other differences between cast iron and wrought iron. The primary difference lies in their production methods. Cast iron is made through casting, while wrought iron is made by heating and repeatedly working the iron.
Wrought iron is also stronger than cast iron. Each time it is heated and worked, wrought iron gains strength, which makes it commonly used in commercial applications due to its durability.
While wrought iron is stronger, cast iron is harder. Under pressure or stress, wrought iron can resist deformation better than its cast counterpart.